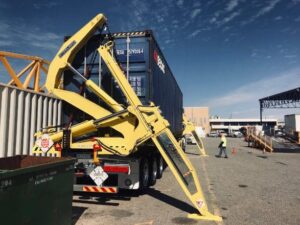
The Steelbro Malaysia operation is proud to celebrate twenty years since its official opening in Kuala Lumpur. I n 1996 Steelbro sidelifters were almost pouring into Malaysia. Customers across the country approved of the technology and appreciated the benefits of being able to load and unload their containers on the ground rather than on the back of a trailer. Transport operators enjoyed major efficiencies as well as safety benefits as there was no longer a need for forklifts to drive up ramps.
Setting up a service workshop was the obvious next move. The operation provided back-up support for the growing number of Steelbro sidelifters and focused on parts supply, repair work, maintenance and the assembly of new sidelifters.
Today the sidelifter has become integral to many transport fleets and the workshop has more than doubled in size. The current team is led by Andy Ersalle, Steelbro’s Regional Manager, South East Asia, and it boasts some impressive experience and expertise among its members.
“The team understands that downtime needs to be kept to a minimum,” says Andy. “We are committed to supporting customers and pride ourselves on producing quality, first class repairs in a quick turnaround time. Factory trained technicians are on hand 24 hours a day, 7 days a week to offer support and service.
“We also place great emphasis on the safety and reliability of all the units we service.” Andy is supported by Hadri Hakim who looks after service sales. Hadri himself has a number of years’ experience in the service and automobile industry.
Azlin, the Workshop Foreman has been with the operation since the early days. In his 18 years working with Steelbro technology, Azlin has handled some of the most complicated repairs, building up valuable experience and knowledge that he shares with the newer members of the team.
There have been a number of changes over the years. Azlin explains, “Today there are more specialised tools available for easier repairs, reference repair manuals are now at hand, as well as the support from the New Zealand head office.”
“I love my job working with Steelbro equipment because it’s quite technical,” says Azlin. “Sometimes I deal with breakdowns – handling sidelifters that are about to collapse or turn over, or fixing a problem with a crane caused by an operator mishandling equipment or by a Prime mover with poor suspension. These customers depend on Steelbro for technical advice and support. I’ve attended a number of these in my years with Steelbro and we generally solve the problem!”
“There are now stronger models available. The old 30 tonne unit has been upgraded to a 45 tonne lifting capacity which is better for tough environments. The high tensile steel that is used today reduces the chance of cracking. There are improved safety features, as well as high quality components used in hydraulic systems that reduce oil leakage.”
Andy explains “We strive to maintain a consistently high level of service for all our customers and have developed some initiatives to help improve servicing capability.”
These initiatives include a comprehensive servicing and after sales support, mobile servicing and service plans tailored to suit individual customer’s needs. Steelbro approved parts can be bought at stable prices and special discounts are available for regular customers and cash buyers.
New sidelifters receive a certificate of fitness, and are subjected to rigorous quality control testing by experienced technical staff. Enhanced one and two year service and maintenance packages are available. These have been introduced to help optimise efficiency, reliability and sidelifter resale value. Packages can be tailored to each customer.
Steelbro has produced imaginative and successful solutions for the container transport industry since 1878. When it comes to embracing technology, Steelbro is an innovator. When Steelbro launched its new sidelifter in the 1980s, the product was a winner and soon the Company gained global visibility.
Continued market success led the company to concentrate resources on the advancement of the sidelifter design. Investment was made in creating designs using the very best materials and components.
High strength steels with superior fatigue toughness from world class steel producers are used. The material is first hardened rapidly by cooling the red hot metal, then heated at lower temperatures and then slowly cooled to eliminate brittleness. The result is a super-tough steel that is the strongest, yet lightest material and the best possible choice for Steelbro’s cranes and chassis.
Steelbro has recently partnered with RUD Lifting Systems for lifting components across the Steelbro sidelifter range. The high quality RUD components will be common to all Steelbro sidelifter models including 16mm ICE chains being fitted as standard. The ICE range offers higher lifting capacity from a much smaller and lighter chain in comparison to existing chains. Due to the advanced control design, Steelbro is able to use the smaller, lighter and more fuel efficient Kubota engines.
Steelbro and its parent company Howard Porter have invested in quality assurance to ensure that products continue to live up to customer expectations. Business management systems are being enhanced to ensure they are aligned with the internationally recognised model for Quality Management Systems, ISO 9001. Owner Howard Porter and Steelbro recently gained ISO 9001 accreditation for its Australia and NZ manufacturing and design operations.
The company is also committed to creating teams for manufacturing, supplier and product improvement. These initiatives take information from manufacturing and post market surveillance activities to help analyse operations and help drive improvement.
These activities all help Steelbro to deliver innovative machines that set the benchmark in value for money, reliability and competitive advantage for the end user.
First published in Asian Trucker Malaysia – Industry Profile